PREPARES PROJECT REPORTS/ MARKET RESEARCH & FEASIBILITY STUDIES SUITED TO THE INDUSTRIAL/ ENTREPRENEURIAL NEEDS
Tuesday 18 December 2012
Thursday 6 December 2012
TextileScreen Printing | ||||
Q | quality and Standards | No standard available for Textile Printing | ||
Uploaded on | August 2007 |
Introduction
Textile printing refers to the production of designs of any kind that could not be made on textile fabrics by normal weaving/knitting techniques. Before the printing process, the cloth should be thoroughly prepared by different wet process namely designing, scouring and bleaching. Printing is mainly done on finished fabrics, curtain clothes, ladies dress materials, bed sheets, bed covers, fabric for children garments, gents shirts etc. to improve its attractiveness, marketability etc. Screen printing can be done in single colour or in combination of different colours as per end use requirement. Colour combination is an important area by which the appearance of an ordinary fabric can be improved to a maximum extent. It is, therefore, necessary that the quality printing material, chemicals and printing screen should be good so that printed items are fully accepted in the market.Market Potential
With regard to marketability of the product in general, printed items have good market potential both in domestic and export market. In populated country like India, there is no problem of marketing printed fabrics as the requirement tends to increase and also these items will satisfy individual customer's needs and requirements in terms of colour combination, design requirements etc.Basis and Presumptions
This project is based on single shift basis and 300 working days in a year and time period for achieving maximum capacity utilisation is considered from 3rd year from the date on which production is started. The Building is of own . The costs of machinery and equipment/material indicated refer to a particular make and approximate to those prevailing at the time of preparation of this project. The cost of installation and electrification is taken @ 10% of cost of machinery and equipment. Nonrefundable deposits, project report cost, trial production, security deposit with State Electricity Board are taken under pre-operative expenses.Depreciation has been considered at 10% on plant and machinery, 20% on office furniture. Interest rate on capital loan has been considered as 13% p er annum.
Implementation Schedule
The implementation period for executing different types of work right from selection of site/working shed and forming of company to selection of market channel and miscellaneous work will take a total period of 5 months. However, on considering that some of the activities may be overlapping, the actual project implementation may hardly take 3 months.Technical Aspects
Process of Manufacture
The various steps involved in printing process are preparation of printing paste, printing of fabric, fixation of dye stuff by curing/steaming, washing off, calendering, folding and packing. Scoured and bleached cotton fabric as obtained from dealers is inspected to remove any objectionable faults and stretched evenly on printing table. Screens containing the designs is placed over the table and the dye paste is pressed over the screen by means of rubber squeezer. The selection of dyes and gums depends on the construction of basic cloth to be printed and their end use. After printing, the printed clothes are cured or steamed for the fixation of the colour. Later, the printed material is thoroughly washed to remove loose dye stuffs. Then, it is calendered, folded and packed for the delivery.Quality Control and Standards
A quality printed item should have good fastness to washing, rubbing and light. This can be achieved by properly fixing the print on the cloth by curing or steaming. Dyes to be used should be of good quality and capable of giving bright shades. Printing quality is not covered by any specifications.Production Capacity (per annum)
Product |
Qty. (Nos.) |
Printed Sarees (Pcs.) | 25,000 |
Printed fabric (Mts.) | 12,500 |
Total | 150000 |
Motive Power
Most of the processes in printing are carried by manual operations as such the requirement of power will be only for running the washing machine, drying heater, fans and lightings. Therefore, 13 HP power will be required to run the unit.Pollution Control
Textile printing does not necessarily produce sufficient effluents (except washing section) so as to create pollution problems. However, a no objection certificate from the State Pollution Control Board is required before setting up of the project.Energy Conservation
Wastage of energy should be minimised as much as possible so that the unit can withstand competition with similar unit.Financial Aspects
Fixed Capital
Land and Building | ||
Land 400sq.mt. @ Rs. 3000p.s.m. Amounting Rs 1200000.00 | ||
Building Area | ||
Factory shed | 200 sq. mt. | |
Store (Raw material) | 50 sq. mt. | |
Store (Finished goods) | 50 sq. mt. | |
Office etc. | 25 sq. mt. | |
Total Covered Area | 325 sq. mt. | |
Total Construction Cost @ Rs. 4000/sq.mt. | 1300000 | |
Total Investment in land and Building | 2500000 |
Machinery and Equipments
Description |
No. |
Rate (Rs.) |
Amount (Rs.) |
Printing Table with AC Top 20'×15'×3' | 1 | 20000 | 80000 |
Rubber squeezers 30 cms. | 15 | 500 | 7500 |
Cottage steamer | 1 | 75000 | 75000 |
Open width jigger | 1 | 150000 | 150000 |
Cylinder drying machine | 1 | 300000 | 300000 |
Baby boiler | 1 | 160000 | 160000 |
Wash room trolleys | 3 | 9000 | 27000 |
Dye paste stirrer | 3 | 3000 | 9000 |
Weighing balance (Dial model) | 1 | 35000 | 35000 |
Water Storage Tank, Bore well | 100000 | 100000 | |
Total | 943500 |
Other Fixed Assets |
(Rs.) |
Erection and installation | 40000 |
Office furniture | 80000 |
Pre-operative expenses | 30000 |
Total | 150000 |
Total Fixed Capital | 3593500 |
Working Capital (per month)
Staff and Labour Wages
Designation |
Nos. |
Salary (Rs.) |
Amount (Rs.) |
Manager | 1 | 16000 | 16000 |
Accountant/Casher | 1 | 6000 | 6000 |
Store-keeper | 8 | 4000 | 4000 |
Peon | 6 | 3000 | 3000 |
Watchman | 1 | 3500 | 3500 |
Total | 32500 | ||
Production Staff | 1 | 4000 | 4000 |
Skilled workers | 8 | 5000 | 40000 |
Artist-cum-stencil maker | 1 | 7000 | 7000 |
Total | 96500 | ||
Production Staff | 1 | 4000 | 4000 |
Pre-requisite 20% | 19300 | ||
Pre-requisite 20% | 19300 | ||
G. Total | 115800 |
Raw Material
Description |
Unit |
Rate/ Unit (Rs.) |
Amount (Rs.) |
Mull Mull cloth bleached 5.5 mtr.×130cm. (mts.) | 11460 | 25 | 286500 |
Dyes (Kgs.) | 13 | 180 | 2340 |
Gums (Kgs.) | 46 | 25 | 1150 |
Chemical and Auxiliaries | LS | 8000 | |
Thickener (Kgs.) Thickener (Kgs.) | 50 | 18 | 900 |
Total | 298890 |
Utilities |
(Rs.) |
Electricity | 7500 |
Coal and fire wood | 2000 |
Total | 9500 |
Other Contingent Expenses (per month) |
(Rs.) |
Postage/stationery | 1000 |
Repair and replacement | 2000 |
Transport/travelling charges | 5000 |
Insurance | 300 |
Miscellaneous expenses | 3000 |
Screens | 5000 |
Total | 16300 |
Total Recurring Expenses (per month) | 440490 |
Total Working Capital for 2 months | 880980 |
Total Capital Investment
Land , Machinery and equipment | 3593500 |
Working capital for 2 months | 880980 |
Total | 4474480 |
Machinery Utilisation
Capacity utilisation is considered as 75% of installed capacity as the utilisation mainly depends on the skill of the labour force employed.Financial Analysis
Cost of Production (per year) |
(Rs.) |
Recurring expenses | 5285880 |
Depreciation on Building @ 5 % | 125000 |
Depreciation on machinery @ 10% | 94350 |
Depreciation on office furniture @ 20% | 16000 |
Interest on total investment @ 13 % | 581682.4 |
Total | 6102912.4 |
Turnover (per year) (Sales)
Turnover (per year) (Sales) |
Turnover (per year) (Sales) |
Rate (Rs.) |
Amount (Rs.) |
Sarees | 25000 | 220 | 5500000 |
Printed fabric (mts.) (on job work) | 12500 | 78 | 975000 |
Total | 6475000 |
Net Profit (per year) | 372087.6 |
Net Profit Ratio (Net profit/Turnover per year) | 5.75 |
Rate of Return on Investment (Net profit/Total Capital Investment) | 8.32 |
Break-even Point
Fixed Cost |
(Rs.) |
Depreciation | 235350 |
Interest on capital investment | 581682.4 |
40% of wages of staff and labour | 555840 |
40% of other contingent expenses | 76800 |
Insurance | 3600 |
Total | 1453272 |
B.E.P. | FC ×100 --------------- FC+Profit = 79.62% |
Monday 19 November 2012
Cement Concrete Tiles and Paving Blocks
Introduction
Cement concrete tiles and paving blocks are precast solid products made out of cement concrete. The product is made in various sizes and shapes viz. rectangular, square and round blocks of different dimensions with designs for interlocking of adjacent tiles blocks. The raw materials required for manufacture of the product are portland cement and aggregates which are available locally in every part of the country.Market Potential
Cement concrete tiles and paving blocks find applications in pavements, footpaths, gardens, passenger waiting sheds, bus-stops, industry and other public places. The product is commonly used in urban areas for the aboveapplications. Hence, the unit may be set up in urban and semi-urban areas, near the market.A lot of face-lift is being given to roads, footpaths along the roadside. Concrete paving blocks are ideal materials on the footpaths for easy laying, better look and finish. Whereas the tiles find extensive use outside the large building and houses, lots of these materials are also used in flooring in the open areas of public offices and commercial buildings and residential apartments.
Basis and Presumptions
Efficiency: It is envisaged that the unit will run on two shift a day for 25 days in a month or 300 days in a year. 75 percent efficiency of machinery and manpower is considered.Time Period: Full capacity utilization is expected to be achieved within 12 months of commencement of commercial production.
Labour Wages: Minimum applicable wages are considered.
Interest Rate: An interest rate of 12% per annum on the total capital investment has been considered.
Margin Money:Promoter is expected to bring in 25% of the total capital investment.
Pay Back Period:The project will have a payback period of about 3-4 years.
Land and Construction Cost: Land cost is considered at Rs. 4000 per square meter, and Construction cost for office and stores at Rs. 9000.00 per square meter, and work shed at Rs. 6000 per square meter.
Implementation Schedule
Activity |
Period |
Preparation of the project report, selection of site, provisional registration from DIC, availability of finance | 2 months |
Construction of building, procurement of machinery and equipment, availability of electrical power | 3 months |
Erection and commissioning, recruitment of manpower, trial runs and commencement of commercial production | 1 month |
Total implementation period | 50000 |
Technical Aspects
Process of Manufacture
Cement concrete is a mixture of portland cement, aggregates (sand and stone chips) and water. Aggregates passing through 4.7 mm IS sieve are known as fine aggregates and the aggregates retained on this sieve are coarse aggregates.The process of manufacture of cement concrete paving blocks involves the following steps:
- Proportioning
- Mixing
- Compacting
- Curing
- Drying
All the raw materials are placed in a concrete mixer and the mixer is rotated for 15 minutes. The prepared mix is discharged from the mixer and consumed in the next 30 minutes. Vibrating table may be used for compacting the concrete mix in the moulds of desired sizes and shapes. After compacting the blocks are demoulded and kept for 24 hours in a shelter away from direct sun and winds.
The blocks thus hardened are cured with water to permit complete moisturisation for 14 to 21 days. Water in the curing tanks is changed every 3 to 4 days. After curing, the blocks are dried in natural atmosphere and sent for use.
The concrete paving blocks gain good strength during the first 3 days of curing and maximum gains in strengths are secured in the first 10 to 15 days of curing. After curing, blocks are allowed to dry in shade so that the initial shrinkage of the blocks is completed before they are used in the work. A drying period of 7 to 15 days would normally complete the drying shrinkage after which they can be used. The concrete tiles are similarly produced with the help of semi-dry pressing of the mixture and allowed to set for 24-36 hours. It is cured in the tanks for 15 days. If need be water can also be sprinkled to gain maximum physical strength in 15-21 days.
Quality Control and Standards
a) Indian Standard SpecificationThere is no Indian Standard Specification specifically on cement concrete paving blocks. However, the specifications laid down in IS 2185 (Part 1) Specification for concrete masonry units: Part 1 for Hollow and Solid concrete blocks, may be used as general guidelines for meeting the quality parameters, since the paving blocks are also essentially solid cement concrete blocks.
b) Quality Requirements
Proportioning of raw materials, mixing, compacting, curing and drying are the important stages of manufacture.
Quality parameters like actual proportion of the individual raw materials, ratio of coarse aggregates to fine aggregates, water to cement ratio, good finish, accuracy in size and shape and compression strength after curing are the some of the important parameters that should be checked periodically to ensure good quality of the product.
Production Capacity (per annum)
Quantity : 800 tonnesValue : Rs. 22,00,000
Motive Power 80HP.
Pollution Control
Dust collecting unit is required to be installed at the mixing and raw material handling section. The workers may use dust masks.Energy Conservation
General maintenance of the machine and drive system can be employed for saving energy.Financial Aspects
A. Fixed Capital
(i) Land and Building
Particulars |
Sq. Meters |
Rate (Rs.) |
Value (Rs.) |
Land | 2000 | 4000 | 80,00,000 |
Built up area | |||
Office, raw material and finished product stores, D.G. set room, water bore well, boundary wall gates, security room and workers room etc. | 500 | 40,00,000 | |
Working Shed | 500 | 6,000 | 30,00,000 |
Total | 1,50,00,000 |
(ii) Machinery and Equipments
Description |
Imp/Ind. |
Qty. (Nos.) |
Rate (Rs.) |
Value (Rs.) |
Production Unit | ||||
Concrete mixer: capacity 10cft/7cft with 3 hp motor, speed of the mixer drum 20 rpm, and other accessories | Ind. | 1 | 4,00,000 | 4,00,000 |
Hydraulically operated Concrete block making machine: capacity 1500 blocks per shift, with pressure vibration technique for compaction, 3 HP motor, and other accessories | Ind. | 1 | 6,00,000 | 6,00,000 |
Mechanical tile melting press with 7HP motor | 1 | 4,00,000 | 4,00,000 | |
Construction of curing tanks | Ind. | 4 | 2,50,000 | 10,00,000 |
Mould tools, weighing scale etc., electrical generator and electrical system, and pollution control system and laboratory | 2 Nos. | 23.00,000 | ||
Water pump set with tube well, water storage tank, | Ind. | 1 | 2,00,000 | 2,00,000 |
Cost of erection, installation lump sum | 5,00,000 | |||
Cost of office equipment, furniture etc. | 1 No. | 8,00,000 | ||
Total | 57,00,000 |
(iii) Pre-Operative Expenses (per month) |
(Rs.) |
Project report cost, non-refundable deposits, etc. | 3,00,000 |
Total Fixed Capital (i+ii+iii) | 2,10,00,000 |
B. Working Capital (per month)
Personnel (per month)
Designation |
Nos. |
Salary / (Rs.) |
Total (Rs.) |
Administrative Staff | |||
Manager-Cum-Technical Expert | 1 | 15,000 | 15,000 |
Supervisor and sales man | 2 | 10,000 | 20,000 |
Clerk-Cum-Cashier and finance man | 2 | 15,000 | |
Store Keeper | 1 | 5000 | 5,000 |
Technical (Skilled and Unskilled Workers) | |||
Skilled workers | 8 | 5,000 | 40,000 |
Semi-skilled workers | 8 | 4,000 | 32,000 |
Unskilled workers | 12 | 3,500 | 42,000 |
Peon | 2 | 3,000 | 6,000 |
Chowkidar | 4 | 3,000 | 12,000 |
Total | 1,87,000 | ||
+22% perquisites on salary | 41,000 | ||
Total | 2,28,000 |
Raw Material (per month)
Particular |
Qty. (MT) |
Rate (Rs.) |
Value (Rs.) |
Lime stone blocks (including transport charges | 1600 M.T. | 500 | 8,00,000 |
Packing material like gunny bags etc. | L.S. | L.S. | 25,000 |
Total | 8,25,000 |
Utilities (per month)
Particular |
Qty. (MT) |
Rate (Rs.) |
Value (Rs.) |
Power | 6000 kWH | 4.0 | 24,000 |
Fuel/Furnace oil | 150 KL. | 18,000 | 27,00,000 |
Water | |||
Total | 27,24,000 |
Other Contingent Expenses (per month) |
(Rs.) |
Postage and Stationery | 5,000 |
Sales and marketing expenses | 41,000 |
Repair and Maintenance | 41,000 |
Telephone | 5,000 |
Consumable store | 5,000 |
Travelling and Local expenses | 25,000 |
Insurance | 30,000 |
Total | 1,52,000 |
Total Working Capital (per month) |
(Rs.) |
Staff and Labour | 2,28,000 |
Raw material | 8,25,000 |
Utilities | 27,24,000 |
Other Contingent expenses | 1,52,000 |
Total | 39,29,000 |
Working Capital for 3 months | 1,17,87,000 |
Total Capital Investment
Fixed capital | Rs. 1,87,10,000 |
Working capital for 3 months | Rs. 1,17,87,000 |
Total | Rs. 3,04,97,000 |
Financial Analysis
Cost of Production (per annum) |
(Rs.) |
Total recurring cost per annum | 4,71,48,000 |
Depreciation on building @ 5% | 5,00,000 |
Dep. on kiln @ 20% | 2,00,000 |
Dep. on machinery and equips. @ 10% | 5,69,000 |
Dep. on tools fixture, dies, racks @ 25% | 30,000 |
Dep. on office furniture and equips. @ 20% | 60,000 |
Interest on total capital investment @ 12% | 36,60,000 |
Total | 5,21,67,000 |
Turnover (per annum)
Particular |
Qty. (MT) |
Rate (Rs.) |
Value (Rs.) |
Burnt Lime | 16,000 | 4,174 | 6,67,91,000 |
Net Profit (per annum)
Total Turnover – Cost Production Rs. 1,35,36,000 – 1,07,88,428 Rs. 27,47,572 |
Net Profit (per annum)
Total Turnover – Cost Production Rs. 1,35,36,000 – 1,07,88,428 Rs. 27,47,572 |
Rate of Return (per annum)
Net Profit × 100 ------------------------------- Total capital investment 1,46,24,000 × 100 ---------------------- 3,04,97,000 47.9% |
Break-even Point
Fixed Cost (per annum) |
(Rs.) |
Total depreciation | 13,59,000 |
40% of Staff and Labour | 10,94,000 |
40% of utilities and Other Contingent expenses (excluding insurance) | 1,30,15,000 |
Insurance | 3,60,000 |
Interest @ 12% | 36,60,000 |
Total | 19488000 |
B.E.P
Fixed Cost × 100 -------------------------- Fixed Cost + Profit 19488000 × 100 ------------------------------- 19488000 + 1,46,24,000 57.1% |
Wednesday 7 November 2012
Solar Baking Unit
Description
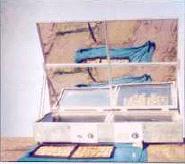
Specifications
Overall Dimensions | |
Length (mm) | 1500 |
Width (mm) | 500 |
Height (mm) | 250 |
Weight (kg) | 29 |
Cooking capacity | 10 persons |
Baking capacity (kg/day) | 2 in winter and 4 in summer |
Time taken in cooking (hrs) | 2.0-2.5 |
Uses
It is used to cook foods and for baking purposes especially during winter in the northern latitudes of India.For further information please contact
Department of Agriculture & Co-operationMinistry of Agriculture, Government of India
224, Krishi Bhavan,
New Delhi - 110 001.
Tel: 23070306 (O)
Composting and Vermicomposting
Introduction
The biodecomposable wastes such as kitchen wastes, if not properly managed decompose creating an insanitary environment conducive to insect breeding and spreading of diseases. While composting is an age old technology, there are limitations due to the longer time periods required for completion of the process. Use of earthworms for faster degradation of partially composted wastes is termed vermicomposting. The technology involves management of the right species of worms under conditions optimal for the vermicomposting process in a time period of 4 weeks or less.Special Features
Can be operated at household, community and twonship level.Prospective Users
Urban and rural households and habitats.Keywords
Kitchen waste, solid waste composting, earthworms, horticultureType of Technology
Process and designFor further information please contact
Managing DirectorFoundation for Innovation and Technology Transfer (FITT)
Indian Institute of Technology, Delhi
Hauz Khas, New Delhi-110016, INDIA
Tel : 91-011-26597167, 26857762, 26581013, 26597153
Fax : 91-011-26851169
E-mail : drkdpn@gmail.com
Fuel Pellets from Municipal Waste
Introduction
In about a decade, major Indian cities such as Delhi, Mumbai, Calcutta will find difficult to dump its daily garbage of more than 5,000 TPD. The existing dumping yards for garbage disposal as land filling would also create enormous pollution and health hazards. The municipal authorities find it expensive to transport and dispose it of scientifically.The Department of Science & Technology (DST) in collaboration with CMC Limited, initiated a pilot project on Integrated Waste Management (IWM) in Mumbai. The project offers a technological solution for disposal of city garbage and provides an option for making environmentally cleaner metropolis. After going through several technology options and assessing marketability of the product, IWM project opted for pelletisation technology over other processes like incineration, bio-gas and compost production, for dealing with this issue scientifically. Over two years of dedicated efforts, involving a great deal of developmental work, have resulted in the establishment of a technology for pelletising the combustibles separated from the municipal garbage.
A prototype fuel pelletisation plant was engineered and erected at Deonar, Mumbai. The production process has been established at the rate of 2 TPH with fuel pellets of high calorific value, which find easy acceptability to industries such as thermal power plants (for boilers with fixed grate, travelling grate, fluidised bed), multi-fuel package boilers for process steam, foundries, restaurants etc.
The process involves primarily, solar drying, separation of incombustible, size reduction and pelletisation, as shown in the following block diagram
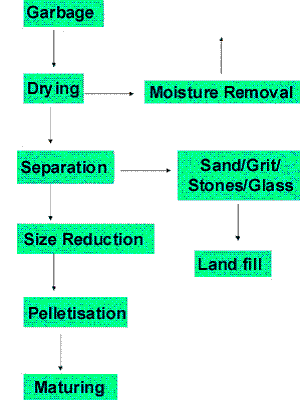
The fuel pellets so produced, are of cylindrical shape catering to a wide variety of end uses. These are hard enough to be transported loose and can be stored like coal.
Characteristics of Fuel Pellets
Size | Dia : 8/20/30 mm, length : 8-40 mm |
Calorific Value | 3500 Kcal/Kg. |
Bulk Density | 0.7 MT per cu. M. |
Density | 1.3 gms./cc |
Ash Content | < 15 % |
Moisture | 10 % (approx.) |
The fuel pellets have several distinct advantages over coal/wood like
- Cleaner fuel, free from incombustiles
- Lower ash content
- Low moisture content
- Uniform size
- Eco-friendly
- Regular, trouble free supply and
- Cost-effective
Plant Highlights
Capacity | 100 TPD fuel pellets |
Raw garbage input | 400-500 TPD |
Connected load | 600 HP |
Land | 2-4 acres |
Working hours per day | 20 |
Working days per year | 250 |
The problem of coal in respect of availability, quality, higher prices etc. can be overcome by using fuel pellets. A number of such plants are currently operating in USA, UK etc. Various grades of fuel pellets have been test marketed at different industries in India to establish the marketability. These are economical and have tremendous market potential in our country.
Learning from above pilot project, TIFAC and CMC have now embarked on the design & installation of a 1000 TPD fuel pelletisation plant from municipal garbage in Hyderabad.
Tuesday 30 October 2012
Safed Musli Agrotechnology
Product and its applications
Safed Musli (Chlorophytum borivilianum Santapau) is a wonder herb which is also known as natural aphrodisiac alternative to Viagra. The dry tuberous roots of the plant are used as tonic for rejuvenating the male reproductive system, impotence, low sperm and in chronic leucorrhoea. In gynaecology, it is reportedly useful during pregnancy as a nutritive tonic for mother and foetus, replenishes lost fluids and improves the quantity and flow of breast milk. Safed Musli is also an ingredient in a number of Ayurvedic & Unani formulations as a restorative for immunity-improvement and remedy for diabetes and arthritis Musli grows naturally in most parts of India under a wide range of temperature and rainfall It can be successfully cultivated as a highly remunerative crop in Uttar Pradesh, Madhya Pradesh, Tamil Nadu, Kerala, Karnataka, Rajasthan, Gujarat, Maharashtra. & the foot hills of Uttarakhand and Himachal Pradesh.Market Potential
The global demand for Safed Musli has been increasing steadily. It ranks sixth among 28 selected priority medicinal plants, the cultivation and export of which is being actively encouraged by the Government of India, through National Medicinal Plants Board. The demand of Safed Musli is estimated at 35,000 tonnes / annum in India while the present supply / collection is about 5,000 tonnes/ annum.Basis and Presumption
- The agricultural land and related infrastructure is available with the entrepreneur.
- Prices are calculated as per the prevailing market rates.
- The yields depend on proper implementation of package of practices.
- Economics of cultivation greatly improves on scale of operation.
- This activity provides tax-free high returns. Additionally a number of government support schemes are available. Latest provisions need to be checked up.
- Market for medicinal plants is volatile and economics may vary from time to time.
Agri practices
Land preparation
Safed Musli requires well drained loamy to sandy loam soil rich in organic matter. Warm and humid climatic condition with good amount of soil moisture during the growing season favour luxuriant vegetative growth and facilitate fleshy root development The land is prepared during April - May. Before that soil is subjected to deep ploughing, tilling during March / April. At least 12 trolleys of farm yard manure per hectare are mixed during April/ May. Raised beds are prepared keeping the bed distance at 60 cm and height 25-30 cm. The raised beds are well irrigated before sowing the planting material.Transplants
It can be propagated through seeds as well as by vegetative means.Propagation by seeds: The seeds are black in colour and with angular edges. It takes 12-16 days to sprout. The seeds are sown in a well prepared seed bed which is manured by using FYM or leaf litter in the first or second week of June. Adequate moisture should be maintained during absence of rain in early part of the season. The seedlings can be transplanted in the field during the next Kharif season at 30x15 cm spacing because the development of plants as well as roots by means of seeds in the first year is not vigorous enough as compared the vegetatively propagated plants.
Vegetative propagation: The initiation of sprouts of fleshy roots starts during late April to mid May. For the purpose of raising plants in the field, the sprouted seedlings are collected after onset of rains and transplanted in the field. The fleshy roots sprout from second week of May to second week of June. The sprouted fleshy propagules are planted in the field in early June, followed by irrigation. The practice of planting on top of the ridges of 15-20 cm height at a row distance of 30x15 cm is adequate for obtaining commercial yield.
Planting
Safed Musli can easily be intercropped with other crops viz. maize, Amla and sapota to enhance profits from the land. The sowing of Safed Musli starts with the first shower of the monsoon. Two to three fingers are approximately attached to a part of crown. The fingers of tuber planting material are treated with fungicides e.g. Bovestin / Streptocyclin before planting in order to keep free from fungus contamination.Fertilization
The FYM is essential to meet nutrient requirements for supporting healthy plant growth.Irrigation
The crop may be sown on outset of rains. If there is no rain after sowing of fleshy root propagules and its transplanting, one irrigation may be provided. Later, when soil moisture recedes in the field, irrigation is required after 10 to 15 days intervals.Weed control
The cropped area should be kept free of weed. One or two hoeings are needed to keep the soil porous and free of weedy growthPest control
Pesticides may be used where necessary to keep Safed Musli crop free from pestsHarvesting
The crop matures in about 90 days after cultivation. On maturity the leaves start yellowing and ultimately dry up from the collar part and fall down. The crop is thus harvested when leaves have dried which occurs during September / October. The bunch of Safed Musli fleshy roots is dug out of soil and washed well with water.Post harvest operations
Drying
The harvested fleshy roots are cleaned and white musli tubers are spread out in the shade for about 4-7 days for drying to about 20% moisture.
Peeling
The roots are peeled manually with a sharp knife to remove the outer skin. It is a tedious job involving manual labour and substantial expenditure. The peeled dry musli is packed and marketed.Yield
About 6 tonnes of wet fleshy root per hectare is harvested. After processing and drying, it is reduced to 1.2 t of peeled dry musli (final marketable product) giving an average yield of 20%.Economics of Safed Musli cultivation per hectare
Particulars |
Amount (Rs.) |
Compost-12 trolleys @Rs. 900 each | 10,800 |
Land preparation+ bed raising | 12,000 |
Planting material 1 tonne or 1 lakh double tubers @ Rs. 3.50 each | 3,50,000 |
Sowing | 8,200 |
Weeding & pest control | 7,000 |
Irrigation & supervision | 9,000 |
Harvesting | 18,000 |
Peeling | 60,000 |
Packing, transportation & misc. | 35,000 |
Total cost of inputs | 5,10,000 |
Total output (1,000 kg peeled, dry roots @ Rs.1,000 / kg) | 10,00,000 |
Net profit | 4,90,000 |
Addresses of Some Dealers in Medicinal plants/ Planting Material
Tropical Forest Research InstituteMandla Road, Jabalpur (M.P.)
Cedmap,
60, Jail Road, Jahangirabad,
Bhopal (M.P.)
KRD Musli Farm,10/47,
Station Road, Rau,
Indore-453331 (M.P.)
Mittal Musli Farm and Research Centre,
Jamod, Jalgaon (Maharashtra)
Regional Research Laboratory
Jorhat, (Assam)
Jeevan Herbs & Agro Farms
178,Keshav Ganj,Sagar (M.P.)
SSSBiotic.com
C/o biosourcing.com (P)Ltd.
A-41, Janpath, Ashoknagar
Bhubaneswar (Orissa)
Kasiraj Exports,
37, Santhai Road,
Tuticorin (TN)
A.Y. Agritec Private Limited
16-7-382/18, Azampura Masjid,
Hyderabad (A.P.)
Thursday 11 October 2012
The Entrepreneur Quiz - What Business Should I Start?
Do you have what it takes to succeed in starting a small business? This interactive entrepreneur quiz will help you assess your Entrepreneurship and Business skills.The first question you should answer when you are thinking of starting a business is "Am I the type?". You will be the most important employee in your small business. It is more important that you rate yourself objectively as the small business owner than how you rate any prospective employee. Appraise your strengths and weaknesses. As a prospective operator of your own small business, acknowledge that you are weak in certain areas and cover the deficiency by either retraining yourself or hiring someone with the necessary skills. The questions in this test indicate to what extent you have the personal traits important to a business proprietor.
Instructions: Read each question and click on one of the suggested answers. Respond by marking the answer that most accurately describes your behavior, feeling or attitude as it actually is, not as you would like it to be, or think it should. You must be absolutely honest with yourself in order to get a valid score.
1. Are You a Self-Starter?
- If someone gets me started, I keep going all right.
- I do things my own way. Nobody needs to tell me to get going.
- Easy does it. I don't put myself out until I have to.
- Most people bug me.
- I like people. I can get along with just about anybody.
- I have enough friends and I don't need anybody else.
2. How Do You Feel About Other People?
3. Can You Lead Others?
- I can get people to do things if I drive them.
- I can get most people to go along with me without much difficulty.
- usually let someone else get things moving.
4. Can You Take Responsibility?
- I'll take over if I have to, but I'd rather let someone else be responsible
- There's always some eager beaver around waiting to show off. I say, let him.
- like to take charge of and see things through.
5. How Good An Organizer Are You?
- like to have a plan before I start. I'm usually the one who lines things up.
- I do all right unless things get too complicated. Then I may cop out.
- I just take things as they come.
6. How Good a Worker Are You?
- I can't see that hard work gets you anywhere.
- I'll work hard for a time, but when I've had enough, that's it.
- can keep going as long as necessary. I don't mind working hard.
7. Can You Make Decisions?
- I can if I have plenty of time. If I have to make up my mind fast, I usually regret it.
- I can make up my mind in a hurry if necessary, and my decision is usually O.K.
- I don't like to be the one who decides things. I'd probably blow it.
8. Can People Trust What You Say?
- I try to be on the level, but sometimes I just say what's easiest.
- They sure can. I don't say things I don't mean.
- What's the sweat if the other fellow doesn't know the difference?
9. Can You Stick With It?
- If I make up my mind to do something, I don't let anything stop me.
- If a job doesn't go right, I turn off. Why beat your brains out?
- I usually finish what I start.
10. Can You Keep Records?
- Records are not important. I know what's need to be known without keeping records.
- I can, but it's more important to get the work out than to shuffle numbers.
- Since they are needed I'll keep records even though I don't want to.
for more details call me---------
How to Set-Up an Enterprise
RENJITH C.O ,ASSISTANT DIRECTOR , INDUSTRIES DEPT KERALA
How to Set-Up an Enterprise
Decision to be an Entrepreneur
The overriding reason for anyone to think of establishing a SSI unit can be summarised in one word - opportunity. An opportunity to be your own boss, to provide a product or service, to implement your ideas, which can generate sufficient surplus, is reason to think of starting up a SSI unit.Starting a small business takes a lot of courage. To be successful - to stay in business - you need a combination of hard work, skill and perseverance.
Choosing your form of Business Organisation
Many first time entrepreneurs do not have a clear perspective of the issues, legal or otherwise, involved in choosing one or the other form of a business. This often results in avoidable mistakes, which later cost time and money to rectify. The options of the form of business with their pros and cons have been explained below. In India setting up a private limited company was the most popular choice among our sample of entrepreneurs.Franchising is also emerging as a major business format. An extensive overview of its features is provided since it is believed that it will grow the same way in India as it has abroad.
Making a Product Choice
Make a careful analysis of the product or service you are choosing, sometimes in short run, there is a shortage of a particular commodity in the market, you may even come to know you will get almost two weeks in advance to supply fresh stock. Does that mean you can jump into that business. First thing in such a condition is to analyse the situation. Keep in mind that shortages may occur due to a number of reasons and a good entrepreneur always examine the pros and cons before setting up a business. It may tempt you to think that perhaps you have found a good businesses idea. But do not be easily influenced by these temporary shortages. Carefully analyse the future demand-supply position of the product, say for the next 3 to 5 years. Only when you are certain that the shortage will remain there for considerable period of time and you would be able to generate enough profits in the very first or second year of operation and that you can produce quality item within an acceptable pricing, then only you should venture into such a business.Location of Industry
After deciding the issues of product, the next important question is, where to set up the unit ? For many tiny units and service-based units, the home is perhaps the best starting point. But not all type of SSI can be set up in home either due to size or due to nature of the industry. Then the entrepreneurs may like to locate their business in industrial estates, areas, parks, complexes developed by concerned state government organisation or private bodies or in a privately leased land subject to approvals by various state and municipal bodies.State level Government agencies like DSIDC, HPSIDC, GIDC, TIDCO, UPSIDC assist entrepreneurs in identifying suitable locations/sites for the project, besides helping in the process of getting all the necessary clearances for the project.
Preparation of Business Plan
A Business Plan is an document where you plan your Business to have an organized and effective response to a situation which may arise in future. Business plan is not just for a start up company but also for those, which are growing. It can be used it to establish realistic goals or targets to achieve and to determine the current position.Start a business plan with describing your business and product or services. Tell about the market you are targeting and the stage of development your company.
Sourcing Process, Raw Materials, Machineries and Equipments
Choices of process technology emerge once the product is finalised. For some complex products, process know-how has to be imported. In such cases agreements for technology transfer should be made with due care to safeguard interest. A lot of appropriate technology is being developed at CSIR and Defence Research Labs and some of these technologies can now be bought. There are some intermediaries like APCTT, TBSE, which can help you to locate the relevant technologies. Besides there are some In-house R & D centres of companies, which develop technologies and sell them to interested parties. Indigenously developed process know-how has intrinsic benefits such as appropriateness, relative inexpensiveness and possibility to work with technology developer.Infrastructure - Land & Building, Water and Power Supply
Once an industrial plot for the unit is secured, then the next job is that of finding a suitable architect to design the outlay of area and factory. Design of factory building has to be in consonance with the type of industry. Have an appropriate plant layout. If you are setting business in home, plan the area, which is to be used as your production centre or office judiciously. You may like to take help of a professional to ensure that the area is utilised optimally.An architect's estimate of building construction is essential for loan applications. Further, architect's certificate for money spent on building is needed for disbursement of loan.
Legal Aspects
Few simple steps to take care of legal aspects of setting business are to Register your unit with relevant organisation, check out the labour laws that would be applicable to you, pay your commercial taxes and taking care of environmental aspects. Each of these aspects is discussed in details.Finance and Working Capital to Start Business
To start and set up their business all SSI units need monetary support. Before seeking fund estimate the cost including that of working capital required for a minimum of 6-8 months and always keep a provision for buffer. you can take help of an CA or concerned officials in Entrepreneurship Development Institutes to work out the total financial cost of your project. Decide the form in which you are going to raise the capital i.e. should it be equity finance, debt finance, loans or a combination of these.Human Resource
Human Resource is an important element to be kept in consideration while setting up an business. Though, projections for manpower and staffing are made in the project report, however it is necessary to time the induction of manpower in a planned manner. For example: The engineers and operatives must be available before the installation of the machinery. While planning for manpower following points should be kept in consideration.Production
Today's competitive market, it is difficult to maintain stable relationships with suppliers, customers, brokers, distributors, and even your own company personnel. Competitors are stealing your best customers. To maintain the edge entrepreneurs need to synchronies their production process, capacity, and delivery schedule.Plan out your work area keeping in mind the requirement of your business. More often than not the area available to small businesses is limited and within that area all the work needs to be carried out, right from storing the raw materials to the final product. The space for each of these should be clearly chalked out.
Pricing
In India, price is often affected by excise duty, sales tax and local taxes like octroi, thereby making it difficult to maintain a uniform price throughout the country. You may opt for any of the following policies or modify and combine them depending upon your objective or you can have your own pricing policy.Marketing
Marketing is an important tool to be used while setting up your business. Study, but don't necessarily copy your competitor's moves. Visit their businesses, watch their ads, figure out their strategies, and keep your eyes open. You may not be able to keep up with your competitor's strategy move by move. You should, however, be ready and able to blunt or block the impact of their moves through effective marketing. Then, later, you can make your own offensive move at your own pace.Paying Back Loans and Profit Generation
Manage your cash Flow to pay back your loans, debts or credits. A healthy cash flow is an essential part of any successful business. If you fail to have enough cash to pay your suppliers, creditors, or your employees, chances are you will be out of business very soon. You should pay back the loans so that when you need loans in future, you get one. You can pay the loans or debts as per terms and conditions initially agreed upon, if you can't pay in time inform the creditor, ask for an extension stating the reasons. Proper management of your cash flow will ensure the same and is a very important step in making business successful.Modenisation and Protection from Sickness
Once you have started the production most important aim for long run should be to remain at the forefront of business and avoid being obsolete in terms of products, services or management aspect. Listen and gauge the market, anticipate the future demands. There are many market survey document or market reports published by individual agencies and government departments on this aspect. An entrepreneur can use these as indicative guide to project the future conditions.In face of competitive environment entrepreneur should keep abreast of process and technological changes that are taking place and wherever possible incorporate the changes which could increase the productivity, efficiency and /or reduce the cost of production.
Feedback and Reporting
Have a suitable feedback mechanism in place to learn from experiences, to gain an insight into what is actually happening in your business, if you don't have one develop a suitable mechanism, which suits your necessities. Think of your experiences, when you wanted to know from others how you were performing your jobs or chores or tried to find out how you performed in your a particular assignmentSaturday 6 October 2012
Saturday 15 September 2012
market potential of packaged drinking water in india (kerala)
Water Industry (Distilled water, Packaged Drinking water, Hydropower, Ice, Mineral water, Safe water, Spring water, Wastewater, Water purification, Water resources, Water tank, Water treatment Chemical, Water Softner, Filter)
Water is a key to social equity to environmental stability and to cultural diversity. Water is also firmly linked with health. Pure and safe drinking water has always been a necessity. The tradition and style of serving drinking water, in India, has however changed quite dramatically during the last decade. Almost a decade ago, the introduction of bottled water or “packaged mineral water” has changed the tradition of serving and consuming drinking water. This has ushered in very strongly, the use of polymers or plastics as materials for water storage and distribution.
The categories of bottled water in India are Packaged Natural Mineral Water and Packaged Drinking Water .Bottled water industry,colloquially called,the mineral water industry,is a symbol of new life style emerging in India. The packaged drinking water in India, which is estimated at Rs.850 crores with over 200 brands floating in the market, most of which have restricted territorial distribution. This is a growing market in India as quality consciousness among the consumers is on the rise. The bottled water market is growing at a rapid rate of around 20%.At this growth rate, the Rs 7000million per year market is estimated to overtake the soft drinks market soon. Multinationals, Coca-Cola, Pepsi, Nestle and others are trying to grab a significant share of the market. There are more than 180 brands in the unorganized sector. The small players account for nearly 19% of the total market. The per capita consumption of bottled water in India is less than half a litre per year, compared to 111 litres in France and 45 litres in the US. These points to the future potential beyond the high growth.
Major Players with their brands include Parle Export which introduced Bisleri in India 25 years ago, Parle Agro with Bailley, Godrej Foods with its Golden Valley, Coca-Cola with Kinley, PepsiCo with Aquafina, Nestle India with Perrier, Mohan Meakins and SKN Breweries entered the market with Golden Eagle and Penguin mineral water, respectively.Nonetheless,Bisleri and Bailley,both of Parle Origin ,enjoy about 50% market share and has become almost generic with the product. The premium bottled water market in India has brands like Evian,San Pelligrino,Perrier.
In the market for water purifiers,while Aquaguard from Eureka Forbes,remains the market leader,several others have made it to the market place.Usha Shriram with its Brita water Purifier already established,has launched India’s first digital water purifier-the waterguard Digital in collaboration with Brita GmbH of Germany. HLL has also forayed into the water business,with its water purifier device called Pure.
water Purifiers (residential segment) are growing at 22-25% annually. A high growth rate indicates a good future potential in these sectors. It is a Rs 5 to 6 billion industry,with Aquaguard cornering more than 50% of the market. The rest is divided among Kent RO,Pentair,Ion Exchange and Others.
Saturday 4 August 2012
PROJECTS TO START IN WAYANADU DISTRICT
1. INSTANT
COFFEE
1.Introduction
Instant Coffee is used extensively as a beverages and is employed also as flavouring material. Brooke Bond India Limitted, and Food Specialities Ltd are the key manufactures of Instant Coffee.
2. Market
Coffee is the
national drink and is consumed by all at any time . instant coffee is made by
adding waterand sugar to it so it have high market.
3) process
Coffee is
powdered and mixed with sugar.
4)land
Minimum area
required 1000-1500 sq Ft
5)Raw
material and utilities
Coffee and
sugar
6) plant and
machinery
Sl. no
|
Item
|
Amount
|
1
|
Peeling Machine
|
25 Lakhs
|
2
|
Powdering Machine
|
50 Lakhs
|
3
|
Boilers
|
50 Lakhs
|
4
|
Filters
|
25 Lakhs
|
5
|
Packaging Machine
|
25 Lakhs
|
Total
|
175 Lakhs
|
7)man power
required
Manager -1
Supervisor-1
Workers -10
8)
- A) Working Capital Requirement for One Month
aSalary and wages
b.Raw material 180 Lakhs
c.Utilities Contingencies and other Exp.
9)Total Project Cost
Total Fixed Capital 175
Lakhs
Total Working Capital 180 Lakhs
Total
Cost of Project 355 Lakhs
10)
Net
profit-45%
Break even
point-45%
DSCR-2.3
11)
CONCLUSION
This project
is got high potential in wayanadu district due vast coffee plantations here.
2.CURCUMIN FROM TURMERIC
1.Introduction
Turmeric is native to India. Turmeric is a very important spices in India. The proposed project envisions setting up of processing Curcumin from Turmeric
1. Market
Turmeric is native to Asia and India. It is
very important spice in India, which produces nearly the whole worlds crop and
used 80% of it. It has been used in Indian systems of medicine for a long time.
Turmeric is a very unique and versatile natural plant product combining the
properties of a spice of flavourant, a colourant of brilliant yellow dye,
cosmetic and a drug. Curcumin also protects the liver from a number of toxic
compounds. It has several medicinal properties like stomachic, carnivative,
tonic, blood purifier, vermicide and antiseptic. According to recently larger
use of curcumin in the pharmaceutical and food industries, it is observed that
few private companies are engaged in the manufacturing of curcumin. About more
than 70% of our products are exported to European countries. As a whole it can
be concluded that there is good export demand of it. There is good scope for
new entrepreneurs
3.process
In liquid solid extraction, a solvent is added to
a solid, such as a turmeric root. As the website DSB science explains,
insoluble material is separated by gravity or vacuum filtration, and soluble
material, in this case curcumin, is "extracted" in the solvent. A
sequence of solvents can be used to separate complex mixtures into separate
groups. The filtered solution can then be used as a liquid or the solvent can be
evaporated to recover the extracted material in powder or crystalline form.
4.land-2000 sq ft
4.land-2000 sq ft
Building-1500 sq ft
5.raw material
Turmeric
6.plant and machinery
Sl. no
|
Item
|
Rate
|
Amount
|
1
|
Storage Tanks
|
25 Lakhs
|
106 Lkhs
|
2
|
Extractors
|
32 Lakhs
|
|
3
|
Solvent System
|
45 Lakhs
|
7. ) Working Capital
Requirement for One Month
i. Salary and wages 1,50,000
ii. Raw material
59,00,000
iii. Utilities Contingencies and other Exp. 1,00,000
8) Total Project Cost
Total Fixed Capital 106,00,000
Total Working Capital 61,50,000
Total
Cost of Project 167,50,000
9) Man power requirement
Manager -1
Supervisor-2
Workers -25
10)
Financial indicators
BEP-45%
DSCR-2.5:1
11.CONCLUSION
This project
is got high potential in wayanadu district due to high turmeric cultivation and
marketability.
Subscribe to:
Posts (Atom)